Truly Rapid Response Outside the Supply Chain
With depleting supplies of personal protection equipment (PPE) for front line workers during COVID-19 pandemic, the demand on supply grew sharply, resulting in significantly longer lead times and price increases. Henkel/LOCTITE and Nexa3D worked fast to meet the demand for face shields.
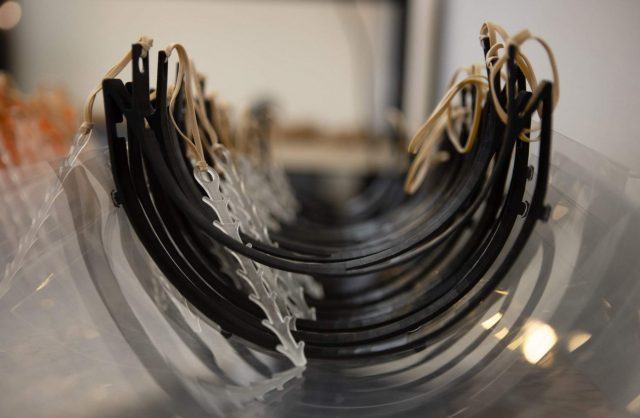
Henkel and LOCTITE have a legacy of transforming processes in multiple industry segments. In the world of additive manufacturing, Henkel is highly regarded for its open source materials platform.
At Henkel, innovative thinking and entrepreneurial spirit are part of the company’s DNA. Henkel and Nexa3D both work to forward the vision of additive manufacturing, making for a natural partnership.
Supply Chains Maxed Out
An increased need for PPE and protection from airborne particles quickly depleted existing supply chains of face shields.
Answering the Call
LOCTITE and Nexa3D leveraged the incredible throughput of the NXE 400 to produce a patented lightweight, durable and comfortable face shield.
Speeding to Production
Nexa3D and Henkel collaborated using a LOCTITE material ideal for producing highly accurate products with a smooth surface finish, even at high print speed. The result was Nexa3D’s XShield and XShield Pro face shields.
Facing a Supply Chain Crisis
In 2020, with the onset of the pandemic, face shields became another layer of essential protection, not only for medical professionals, but for essential workers in retail, utilities, logistics, and other businesses. Face shields provide a clear plastic barrier that covers the wearer’s eyes, nose and mouth, helping protect users from contact with infected droplets and can be used in place of, or conjunction with, a surgical mask for protection.
Traditional manufacturers of face shields, typically catering to the medical sector, were unable to keep pace with the increased need during the first wave of the pandemic. Many companies leaned into the need for additional solutions, including 3D printing materials manufacturer LOCTITE in partnership with Nexa3D.
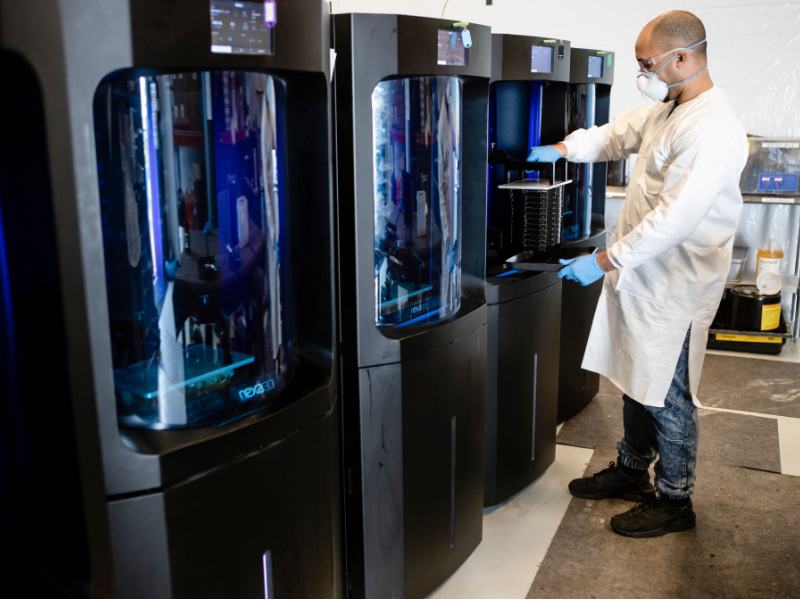
Speeding to Production
Henkel’s Open Materials Platform and focus on agile innovation allowed them to quickly solve big problems by eliminating the long lead times and supply chain strain involved with traditional processes.
Working closely with Nexa3D designers and engineers, the partners chose the material LOCTITE 3D 3843 for its high tensile and flexural accuracy, ideal for producing highly accurate products with a smooth surface finish, even at high print speed.
All that made it the ideal choice for the unique headband design used in Nexa3D’s XShield and XShield Pro series of face shields.
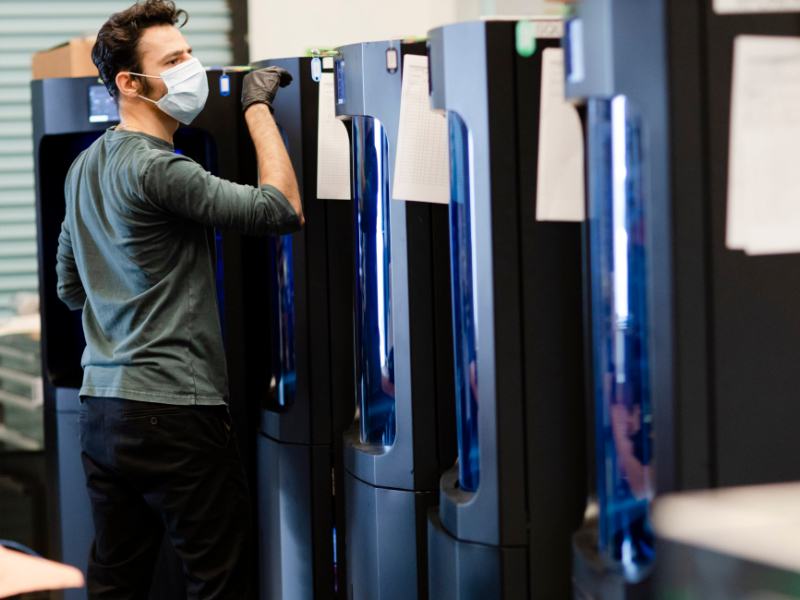
“We believe that the additive manufacturing industry is uniquely positioned to deliver practical, urgent and scalable solutions during this unprecedented crisis.”
Avi Reichental – Nexa3D CEO
Producing Essential Supplies
While the XShield and XShield Pro went through the process of receiving FDA Emergency Authorization, Nexa3D installed additional production capacity at its new customer experience facility in Ventura, California, ramping up capacity to ship over 10,000 units weekly at the height of the pandemic.