Breaking the Mold: Lalaland Speeds Production and Lowers Costs of Footwear Manufacturing with Ultrafast 3D Printing
Lalaland Production and Design, a leading US-based footwear and clothing manufacturer, has recently partnered with Nexa3D to validate its new Thermoplastic Co-Polyesters (TPC) material. Innovation with this opens up significant opportunities to speed up the production of new footwear products, providing increased flexibility in design and lowering costs throughout the process.
Based in Los Angeles, Lalaland offers a full range of services and facilities for producing shoes, handbags, belts, and small leather goods in exotic skin or leather. It provides clients with cost analysis and consulting for onshore product and line development and can carry out the design, sketch, styling, pattern, prototypes, and final sample production.
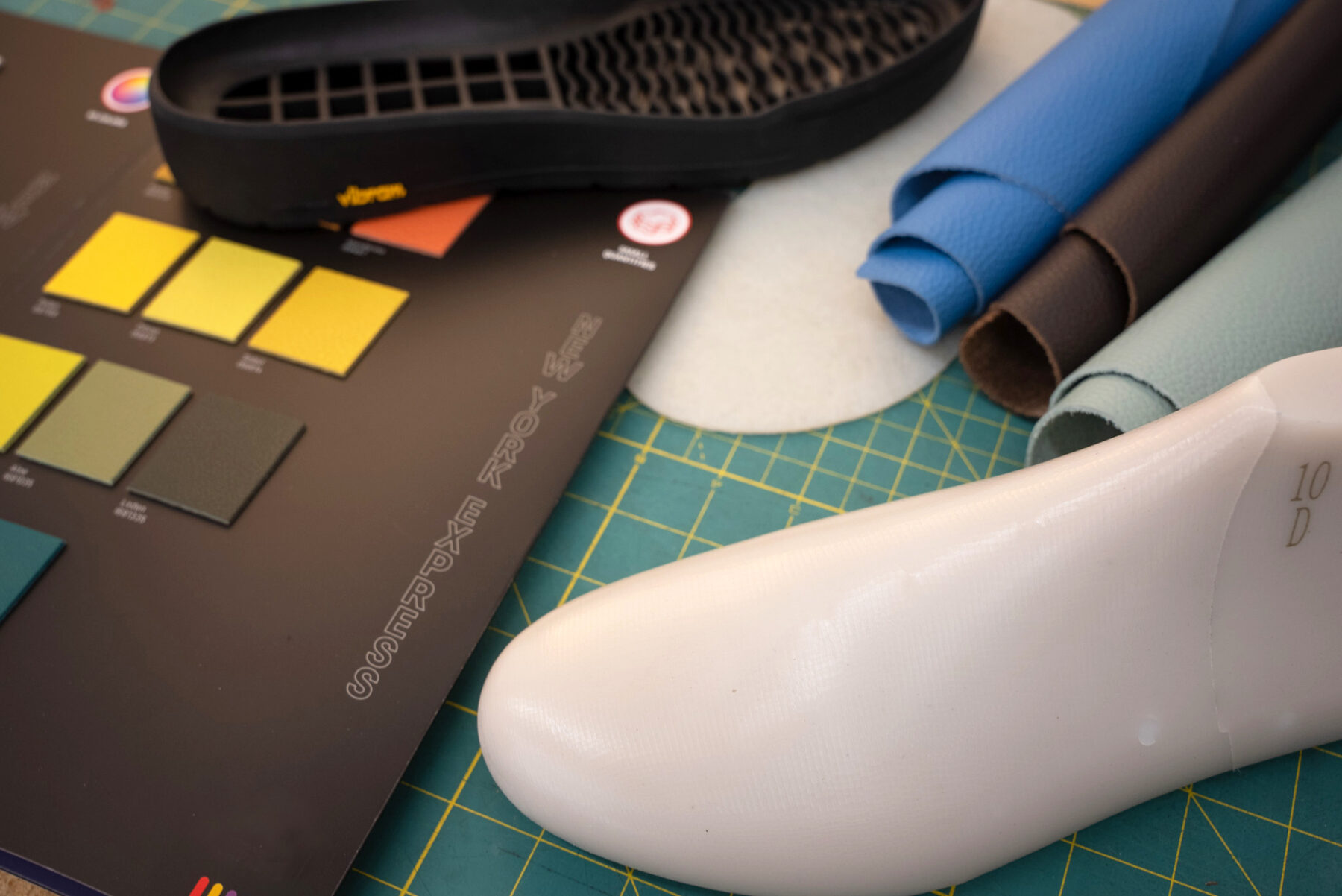
Challenge
Footwear is one of the most challenging markets within the clothing industry for businesses to enter. The demands on the product are very different from other garments, and one of the biggest inhibitors is the design and production of the components, particularly the soles and midsoles of the shoes.
Dwayne Jeon, Director at Lalaland, explains, “Traditionally, we have developed midsoles using EVA injection molding processes. This technique takes around 26 hours to produce a typical midsole, and with a further eight processes to go through, the average turnaround time from design to production is around 18-24 weeks. In addition, you need a mold for each shoe size, so the cost of prototyping new products in all sizes can be well over $50,000. With these high costs, the minimum order quantities have to be in the region of 1,000-2,000 pairs to justify the time and expense in the design process.”
Dwayne shares that Lalaland initially approached 3D printing with cautious optimism, recognizing its potential to expedite processes. “While we were keen to explore 3D printing to speed up our processes, we had seen prolonged production times experienced by our clients when using various 3D printing technologies, including Carbon’s resin printer and HP’s Multi Jet Fusion.”
Customer
Lalaland Production & Design, Inc.
Industry
Footwear
Products
- Nexa3D SLS printer
- Thermoplastic Co-Polyesters (TPC) material
Application
Manufacture footwear midsoles using new innovative designs
Advantages
- Production time of midsole reduced from 26 hours to 3 hours.
- TPC’s durability and mechanical performance enables stronger, longer-lasting, and more customizable midsoles.
- Process automation means a huge reduction in labor time and cost.
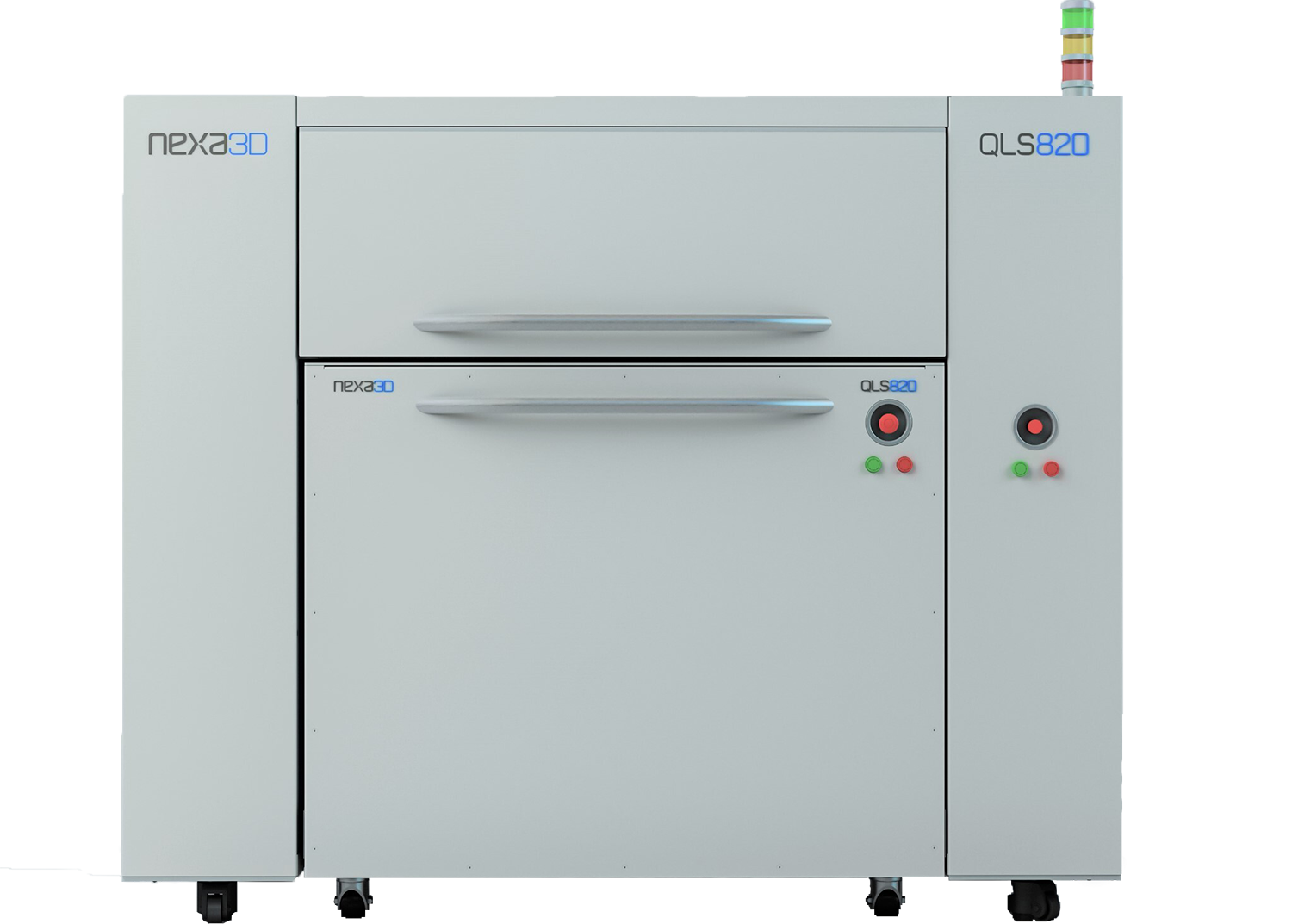
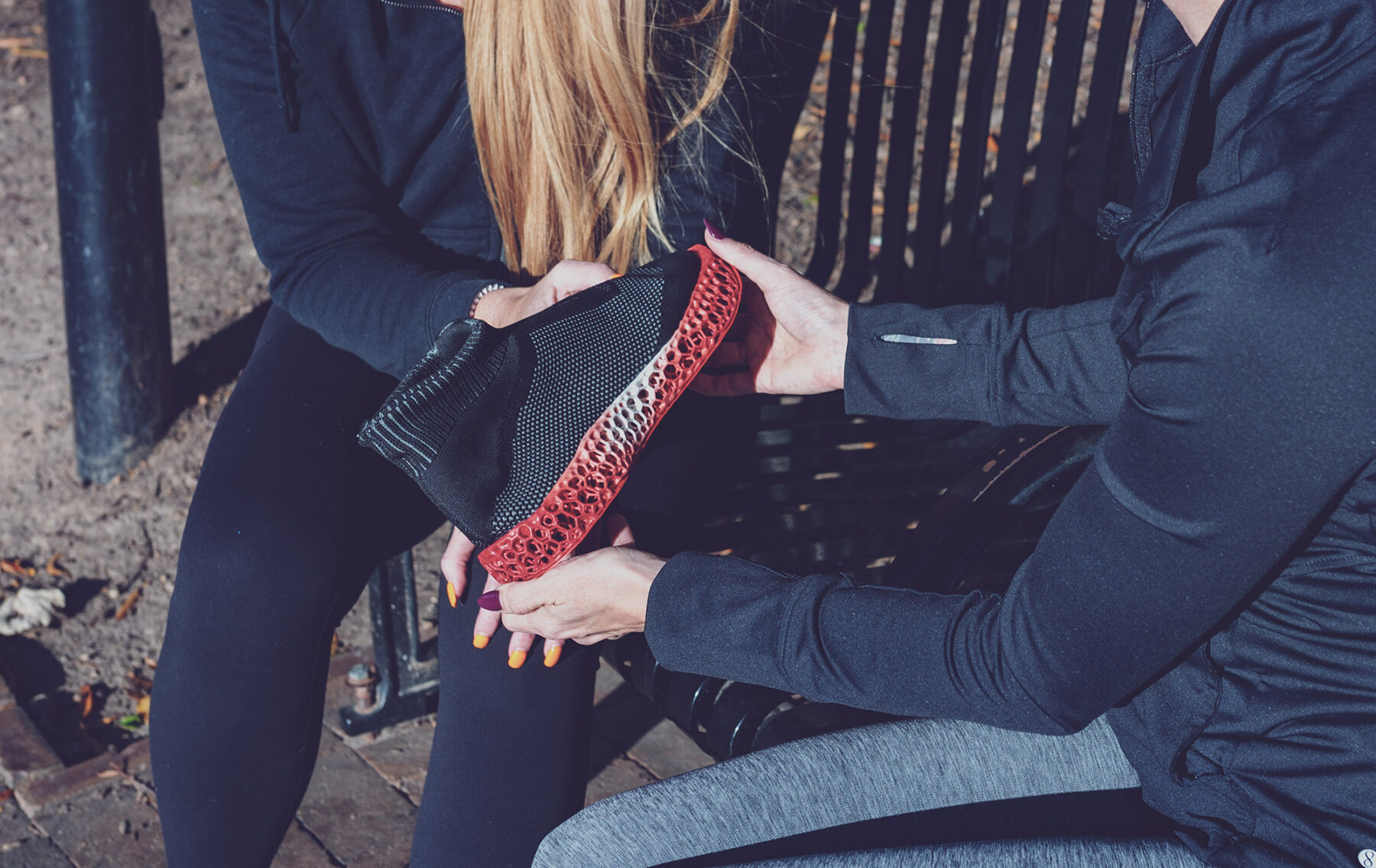
Solution
From 26 hours to produce a single midsole, Lalaland can now reproduce the midsole in just three hours using the Nexa3D SLS printer with TPC material.
“That is such a huge time difference. It immediately revolutionized the prototype production process,” explains Dwayne. He adds, “Another huge benefit was that with the Nexa3D solution, there are no tooling costs. You only pay for the printing. This means we don’t have to restrict ourselves to just one item when we have several concepts to try out. We can produce multiple concepts simultaneously, saving us a lot of time and money and enabling us to deliver a much better service to customers.”
Thanks to Nexa3D’s high-speed SLS 3D printer technology, Lalaland has reduced the process from design to manufacturer from 18/24 weeks down to just four weeks. “This amount of time to produce a product ready for manufacture would be considered impossible in the industry – and we are now achieving it!” notes Dwayne.
TPC high-durability thermoplastic elastomer is great for products requiring both durability and flexibility. TPC also exhibits water resistance, abrasion resistance, excellent rebound, and chemical resistance, making it a fantastic solution for scaled production of elastomeric components.
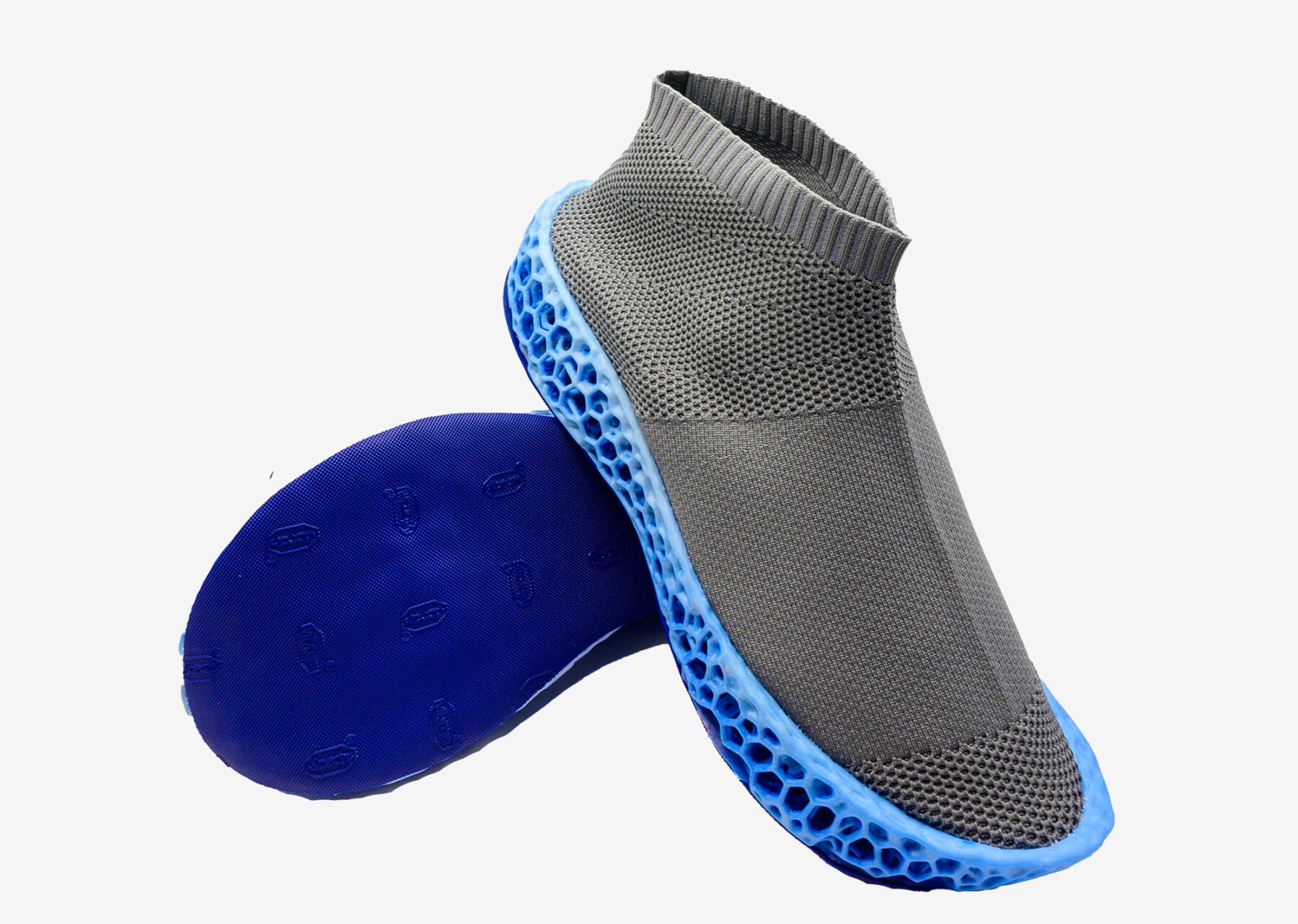
And, of course, leveraging adaptive design techniques like lattice structures, TPC can deliver premium performance while light-weighting footwear and enabling mass customization without significant costs. “Midsoles made using traditional techniques tend to decompress and deform in time and after use. We can manipulate the lattice structure with TPC to fit specific purposes and activities. We can create different lattice sizes for specific requirements, but all within the same overall product design. Previously, this was impossible to do, and it also means a huge saving in time and cost.”
For products being made in the U.S., additive manufacturing helps to reduce the high labor costs. A process like SLS scales well and is supported by a suite of automation solutions to streamline post-processing and maintain low associated labor costs.
Dwayne points out how TPC’s bright white color provides more opportunities to customize color schemes using automated dyeing equipment. “Combining SLS technology from Nexa3D with TPC allows us to have great designs with a huge range of colors. We can even mix colors and gradations for some really cool looks. We could not do this with our previous systems, which limited us to a small amount of pre-determined colors, which isn’t always what customers want.”
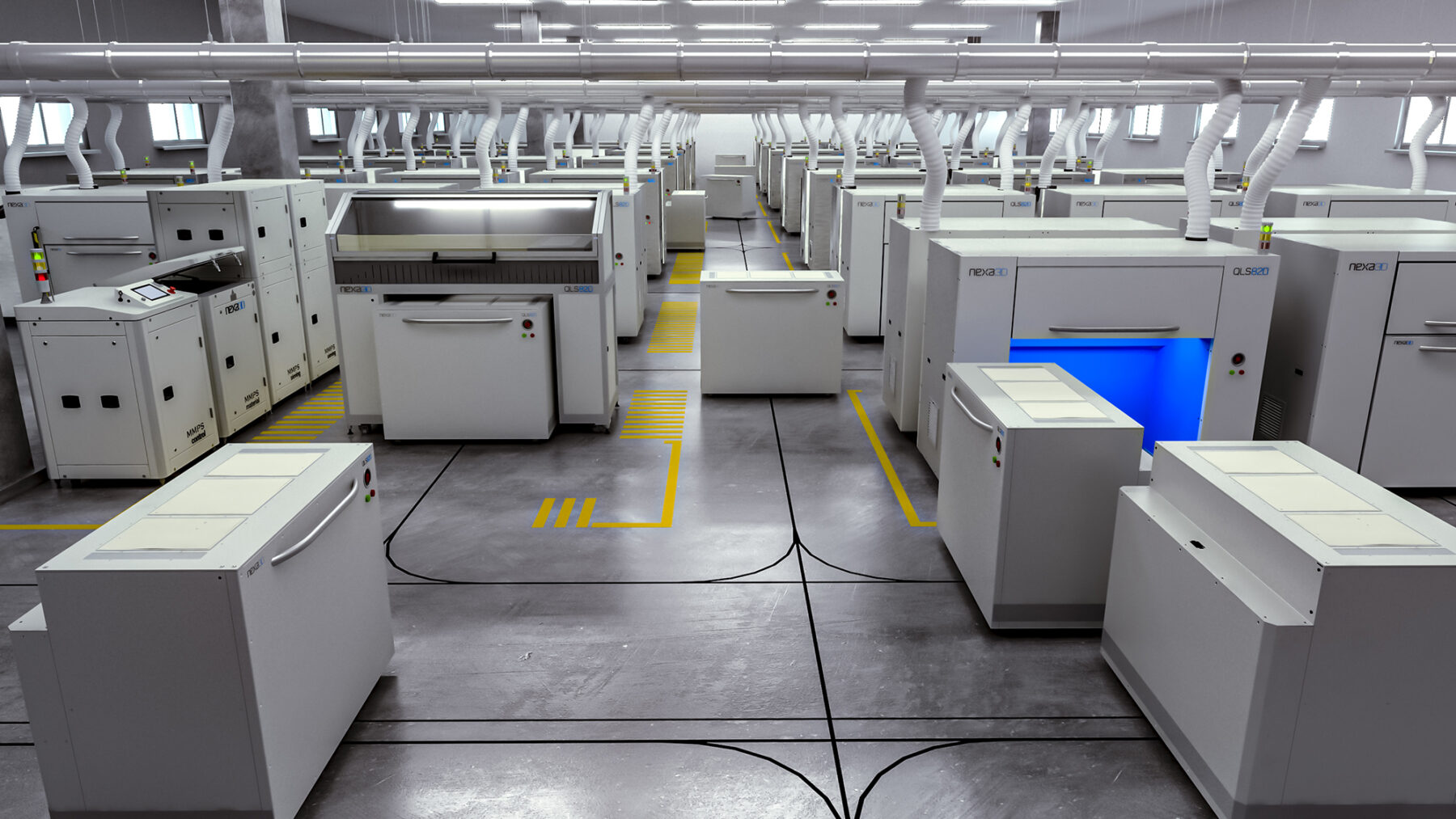
Looking Ahead to Mass Production with SLS
One factor that initially deterred Lalaland from adopting 3D technology was the inability to achieve mass production with other machines. Dwayne highlights the benefits of a high-speed 3D printing solution, “Unlike companies focused solely on concept and R&D, our company specializes in footwear manufacturing. While intriguing 3D prototypes often surface on platforms like Instagram, they rarely reach the market due to impractical mass production limitations. However, with Nexa3D’s printing speed and large build volume, we can produce up to 10 pairs in each build.”
The Nexa3D SLS printer with TPC has revolutionized Lalaland’s ability to design and produce footwear products. It has reduced production time from four months to one and slashed the costs associated with the process. It has also enabled a better standard of product, with more designs, more strength and flexibility, and even more colors.
Dwayne concludes, “This has been a fantastic investment that has had a massively positive impact on our business. We can deliver more and better solutions for our customers faster and at lower cost. We couldn’t really ask for more.”
Ultimate Guide for SLS 3D Printing
Laser Sintering vs. Fusion Sintering—Which Powder Bed Fusion Technology is Best for You?
Download the full guide.