Evonik INFINAM® TPC
Thermoplastic Elastomer Material
INFINAM® TPC exhibits excellent water resistance, abrasion resistance, and UV stability, making it ideal for many industries, including footwear, orthotic and prosthesis, sporting goods, automotive, aerospace, medical, and consumer products.
Technical Datasheet
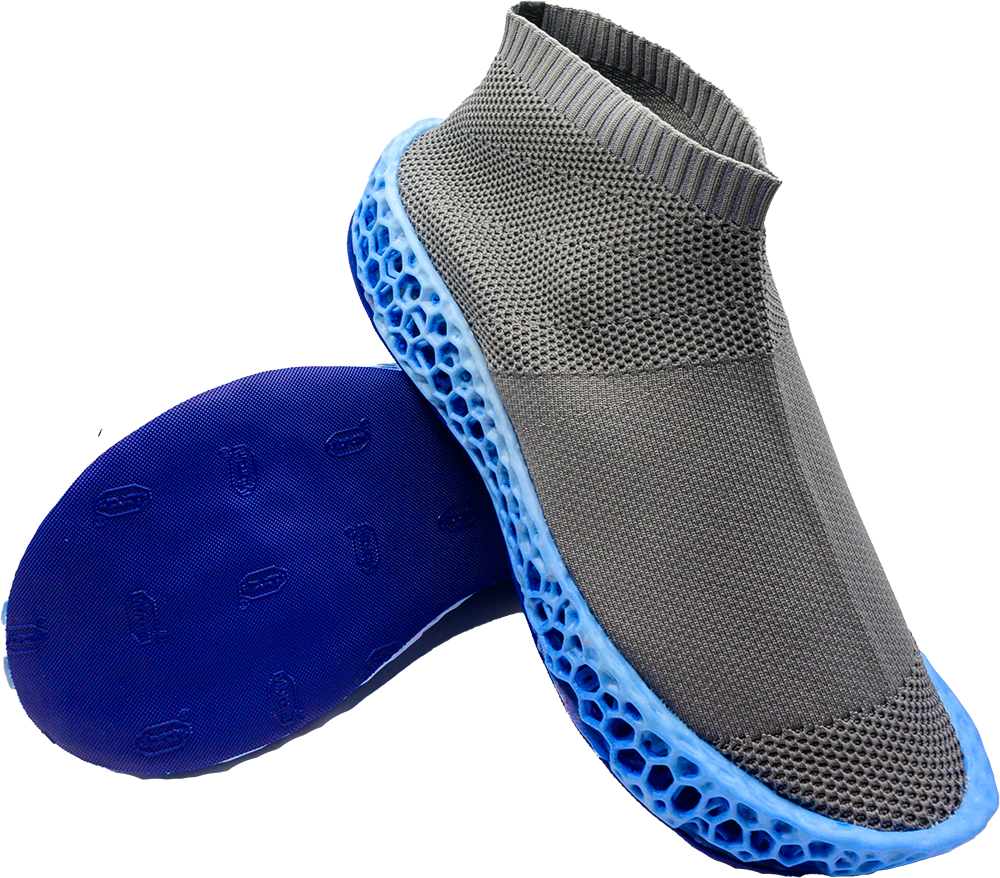
Flexible 3D Printing
3D Printed Airless Basketball
We asked our manufacturing partner JawsTec LLC to put our newly released TPC flexible 3D printing material to the test on their QLS platform. They designed and 3D printed a basketball. Here are the results.
- Tear Strength 130kN/m
- Shore A 95
- High Rebound
- Excellent Energy Return
INFINAM® TPC 8008 P Material Specs
Measurement | Value | Unit | Test Method |
---|---|---|---|
Tensile Modulus | 131 | MPa | ASTM D 638 |
Strain at break | 440 | % | ASTM D 638 |
Tear Strength | 130 | kN/m | ASTM D 624 |
Taber Abrasion Resistance | 117 | mg/1000 cycles | ASTM D 1044 |
DTUL @ 66 psi | 85 | °C | ASTM D 648 |
Hardness (Shore D) | 46 | ASTM D 2240 | |
Melt Flow Index, MFI | 35.7 | g/10min | ASTM D 1238 |
Charpy impact strength, +23°C | N | kJ/m² | ISO 179/1eU |
Charpy impact strength, -30°C | 88 | kJ/m² | ISO 179/1eU |
Exceptional Performance
TPC 8008P enables users to produce prototypes and production components with an exceptional balance of mechanical, thermal, and chemical properties for elastomeric performance that stands the test of time.
Designed to Deliver Results
TPC’s performance characteristics are design-responsive. Employing lattice designs with varied strut diameters, lengths, and densities, TPC can present a range of softer shore A durometers for orthopedics and prosthetics as well as higher durometers for applications like sporting goods.
Superior Serial Production
The versatility of TPC for elastomeric production parts is unmatched. Even with it’s rugged performance, TPC remains easy to post process and delivers consistent results that scale easily as your production needs grow.
Flexible Resin 3D Printing Solution
Key Properties, Performance Characteristics, and Benefits
INFINAM® TPC 8008 P is specifically formulated for use in powder bed fusion technologies like Nexa3D’s QLS series printers. Optimized for surface finish, part quality, and accuracy, this material offers benefits like:
- High elasticity: TPC 8008 P exhibits high elasticity and can be stretched up to several times its original length without breaking.
- Chemical resistance: TPC is highly resistant to a wide range of chemicals, making it suitable for use in a variety of industrial applications.
- Easy to process: TPC is easy to process and can be printed at relatively low temperatures, reducing the risk of warping and other printing defects.
Overall, TPC 8008 P is an excellent choice for a wide array of applications across industries like automotive, aerospace, medical, and consumer products.
Want to know more?
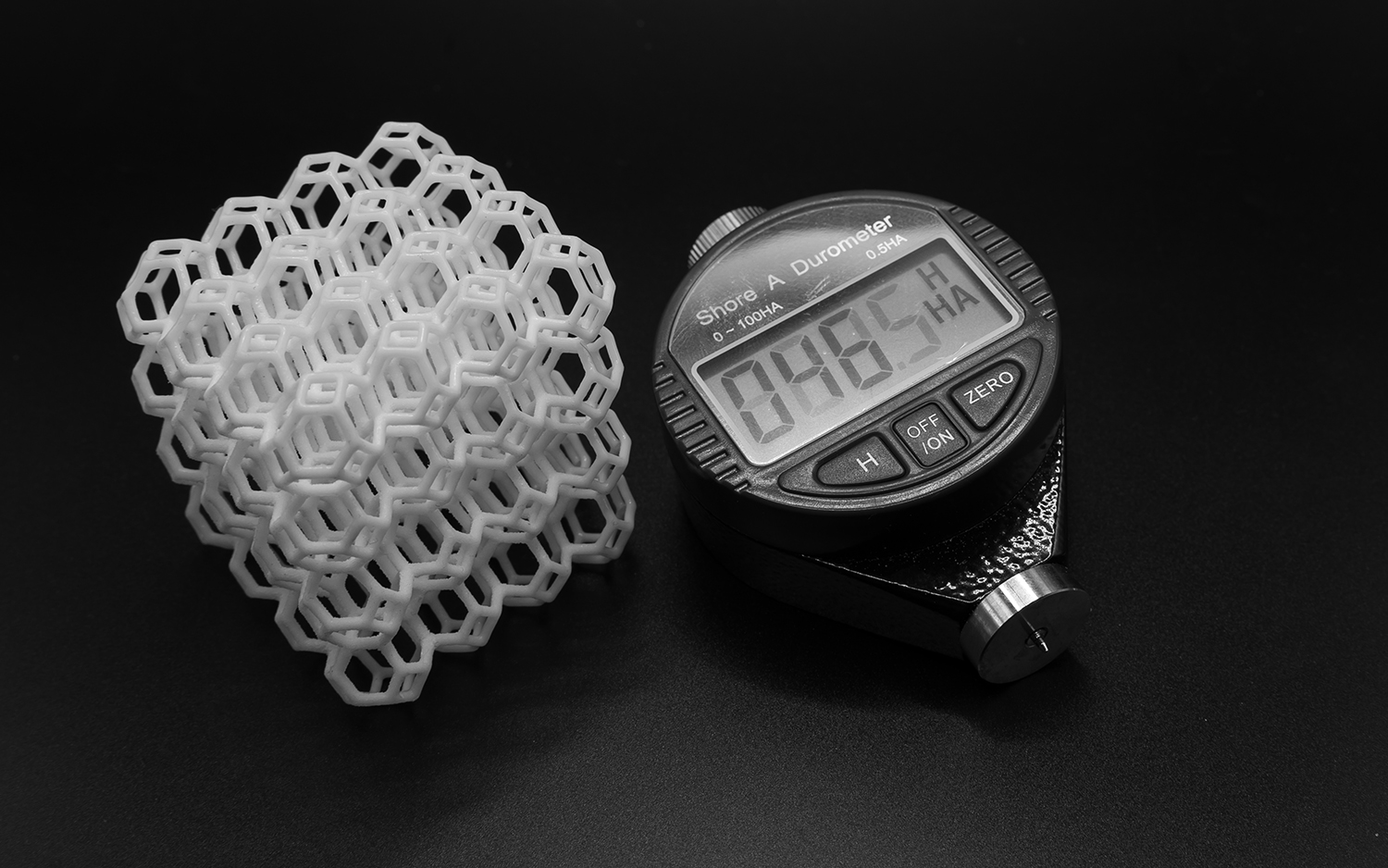
TPC vs TPE and TPU
Elastomeric materials for additive manufacturing are known as thermoplastic elastomers or TPE’s. There are several different chemical compounds within this material category.
Thermoplastic polyurethane (TPU) is the most common type of TPE used in 3D printing. TPU is generally the softest TPE available at Shore 60A-55D. It also is usually the least durable in terms of mechanical toughness. TPU is generally regarded as a prototyping material used to simulate production materials rather than being a production material in and of itself. Generally, softer materials in the Shore 70A range require inert selective laser sintering to reach the lowest Shore A numbers. When TPU is printed on non-inert technology like MJF, Shore A numbers tend to be in the low 90’s. Footwear companies can often use TPU to mimic EVA foam for prototyping.
Thermoplastic Polyamide (TPA) is a chemical co-polymer of TPE and highly flexible nylon. The result is a combination of smoothness and texture from nylon and TPE’s flexibility. TPAs tend to be hygroscopic and harder than TPUs and are not typically used as much in selective laser sintering applications.
Thermoplastic copolyesters (TPC) are copolyether esters with alternating, random-length sequences of either long-chain or short-chain glycols. TPC has been used in industrial applications for decades and is now available for selective laser sintering. TPC has a shore hardness of 95A. It also exhibits much higher mechanical toughness than other TPEs and does require an inert environment for sintering.
Post Processing for TPC
Selective laser sintering is the only choice for production-volume printing with TPC. Printing with SLS allows for significant freedom due to the powder bed, which forgoes support structures. The post-processing of TPC falls into de-powdering and vapor smoothing if desired.
Depowdering can be completed manually through a manual depowdering and powder reclaiming device, or it can be done automatically via post-processing equipment available from several vendors. Once depowdering is completed, TPC can be vapor smoothed if a smooth surface is desired. It should be noted that vapor smoothing can provide increased performance and durability if TPC is selected for thin beamed high displacement meshes.
TPC for Orthotics and Prosthetics
TPC is an ideal candidate for 3D printing orthotics and prosthetics due to its relative softness and durability compared to TPUs. The mechanical toughness of TPC allows parts to be much thinner for fit-sensitive applications like ankle braces and orthotics. The extremely high tear strength enables new design freedom not afforded by TPUs. Thinner, more comfortable human interfaces are reachable with TPC. Color can also be a design criterion for these applications. TPC prints bright white and is ideal for customized production (end-use0 components as it can be easily dyed in any color.Etiam quis rhoncus orci, ut pulvinar odio.
TPC for Footwear and Sporting Goods
TPC is poised to become the performance material of choice for footwear and sporting goods. TPC can provide the performance and durability for these applications that other TPEs have not met, and it provides better processing solutions for scalability.
Footwear and sporting goods applications generally look to advance cushioning and protection performance with meshing and latticing that absorb impact forces. TPC excels when used in shoe midsoles or impact protection in helmets in these high-deflection areas. Using meshes with low beam diameters, users can yield areas of localized shore softness as low as 40-49A! TPC ensures those meshes are tough enough to stand up to repetitive uses that are impossible with other TPEs.
TPC printed with SLS technology also exceeds the performance associated with elastomeric photopolymer resins with better production economics. Using photocuring resins requires support structures and significant chemical cleaning that can also require centrifuges and the generation of a significant chemical waste stream. With these two hurdles, it is clear that selective laser sintering with TPC is the more scalable approach for additive manufacturing in footwear and sporting goods.
Talk to an Expert
Speak to a product expert today so we can learn more about your 3D printing application!