From Offshoring to Desktop Manufacturing
How an acoustic instrument startup shaved production costs by as much as 90% with desktop manufacturing on the XiP
Liquid Sound Technologies is a small business that develops sound enhancing accessories for acoustic instruments from guitars to pianos to drums. Founder Vladimir P Gutsman is an inventor at his core with a mechanical engineering background and has several patents to his name. One such patented product is the Droplet Sound System – a non-invasive set of custom-engineered plates and bridge pins that enhance the resonance and clarity of acoustic guitars.
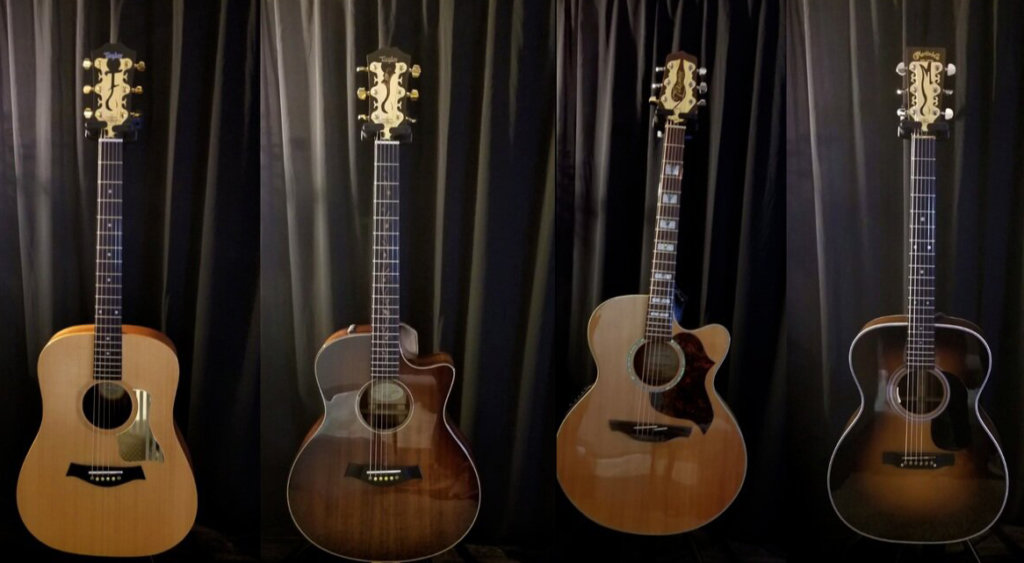
Customer
Liquid Sound Technologies
Industry
Consumer Products – Instrument Accessories
Products
- XiP Desktop 3D Printer
- xCE Black Resin
Application
On-Demand Manufacturing
Advantages
- 90% reduction in part costs
- Lead time reduced from 9 months to 1 day
- High strength – capable of withstanding long-term tensile forces of guitar strings
- High quality and fine feature detail for small threaded parts not possible with FDM 3D printers
- No need for minimum order requirements of 10,000 pieces – saves space and transportation costs, providing additional design iteration flexibility
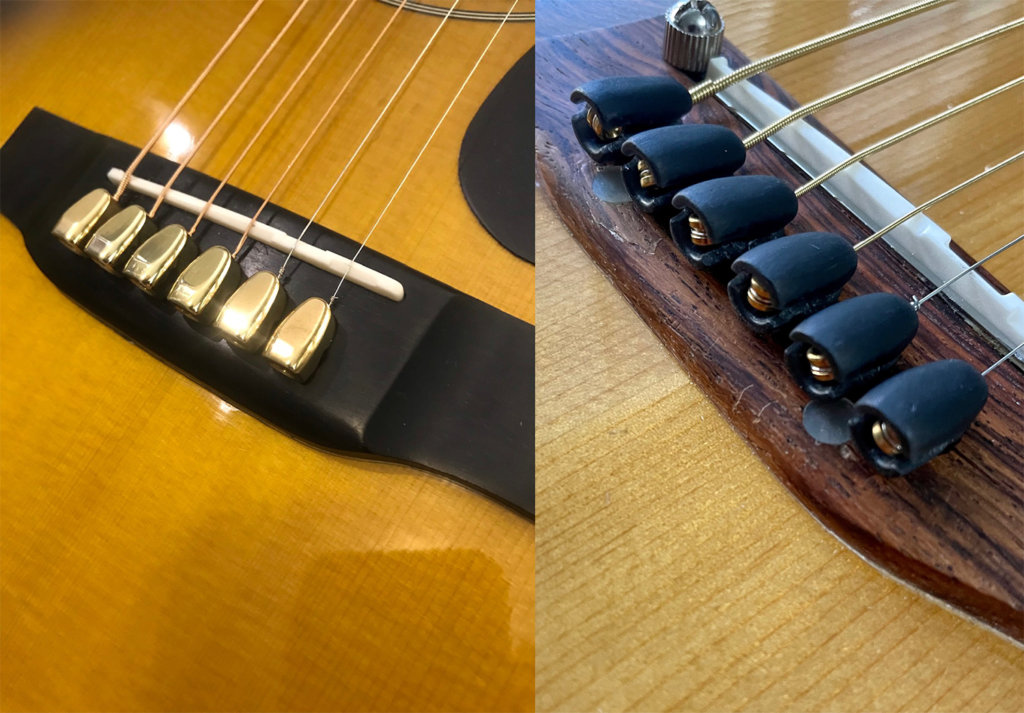
CHALLENGE
Small Business, Large Minimum Order Requirements and Long Lead Times
For many small businesses, ramping up production comes with some major challenges. Small batch orders carry a high per-part price tag. LST’s Droplet Sound System has historically been manufactured in brass. In order to track down competitive pricing, Vlad has tried several service providers – his most recent (and lowest cost) option was based in Taiwan.
To achieve pricing that made sense for his business model he had to order in quantities of 10,000 pieces – a bulk order of machined brass parts that costs roughly $350,000. “A small run for R&D verification we could get in 4 to 8 weeks, but for full production the minimum is 6 months even stateside, and overseas with sea freight shipping, that’s 9 months to a year.”
If LST modifies a design or launches an updated product, they must place the order early, while attempting to sell through the remaining inventory before the next shipment arrives (nine months later). “It’s a huge pill to swallow for a startup.”
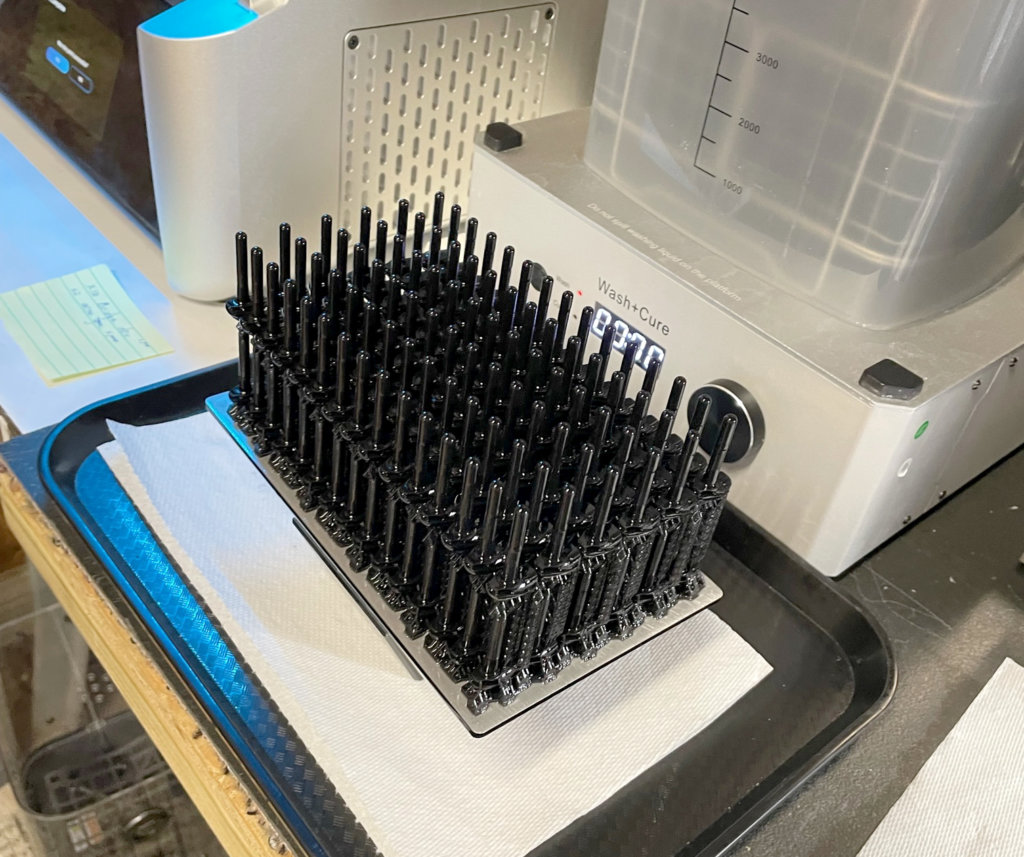
SOLUTION
Manufacturing On-Demand with a Desktop 3D Printer
Vlad is no stranger to 3D printing. He has worked with all manner of industrial 3D printers in past engineering jobs, and in 2016 he purchased his first desktop FDM 3D printer. In-fact, he has grown his collection to a small fleet of FDM machines. He uses these printers for prototyping, but the quality and fine feature detail is not good enough to produce the precision threading – “It’s impossible to manufacture the bridge pin bolts on FDM successfully. Truth be told we were never able to get the bolt print with a clean enough thread and we’ve tried inexpensive and expensive FDM printers, and a wide variety of materials and quite frankly it was a dud.”
That’s when Vlad came across XiP at a trade show. While he also considered two other professional systems, the speed and quality, not to mention the customer service of Nexa3D made the choice an easy one, “When we needed to prove the concept and then prove the application, Nexa3D was three steps ahead of everybody – it was very comforting to know that you have that backing.” Vlad landed specifically on an engineering material called xCE from Nexa3D. The xCE resin is a single cure polymer that has excellent isotropic properties and exhibits long-term environmental stability making it well suited for a variety of functional applications. In Vlad’s case, the xCE proved worthy in extensive strength testing where guitars were over tensioned two tones higher than standard for a period of three months. The parts passed the tests with flying colors.
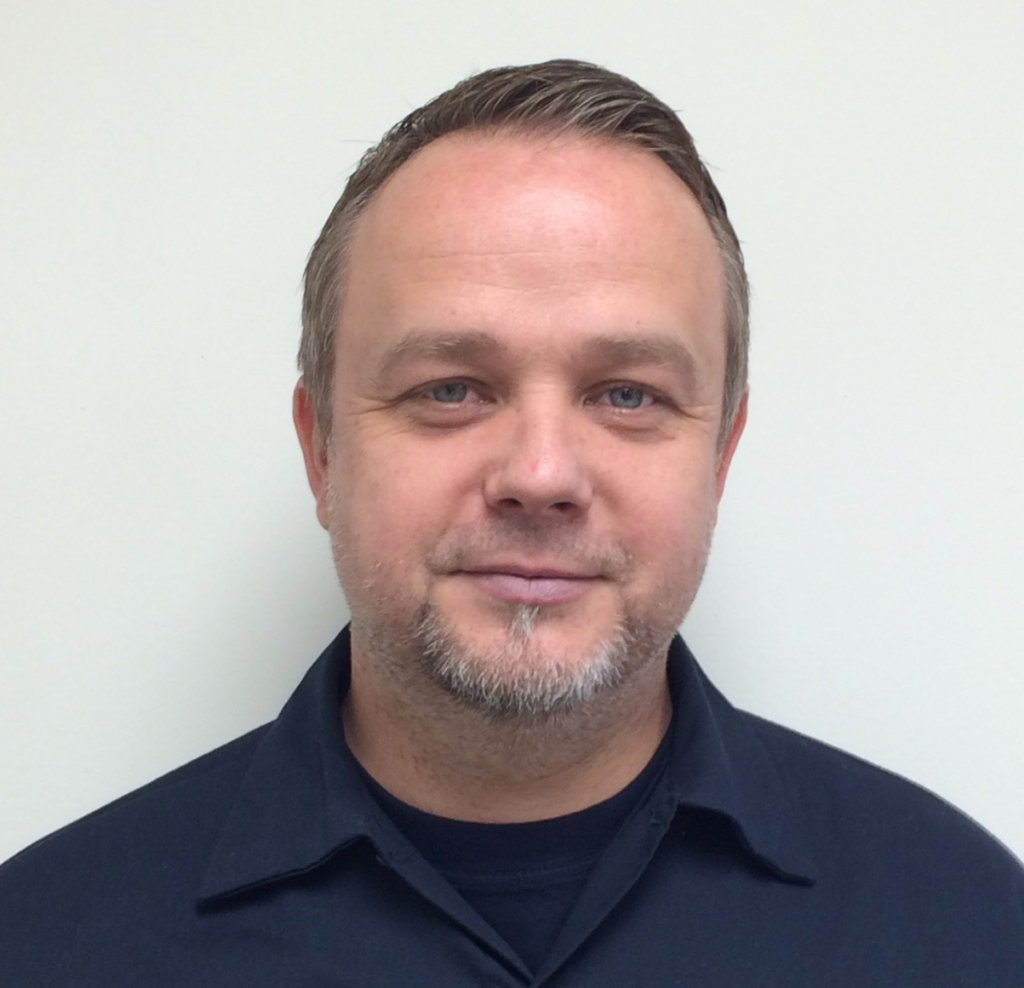
“The biggest benefits of XiP compared to other 3D printers we’ve used are (1) the speed is unmatched, and (2) the variety of materials, from low cost modeling to serious production materials like xPRO and xCE that are literally replacing metal parts for us.”
Vladimir Gutsman, Founder of Liquid Sound Technologies
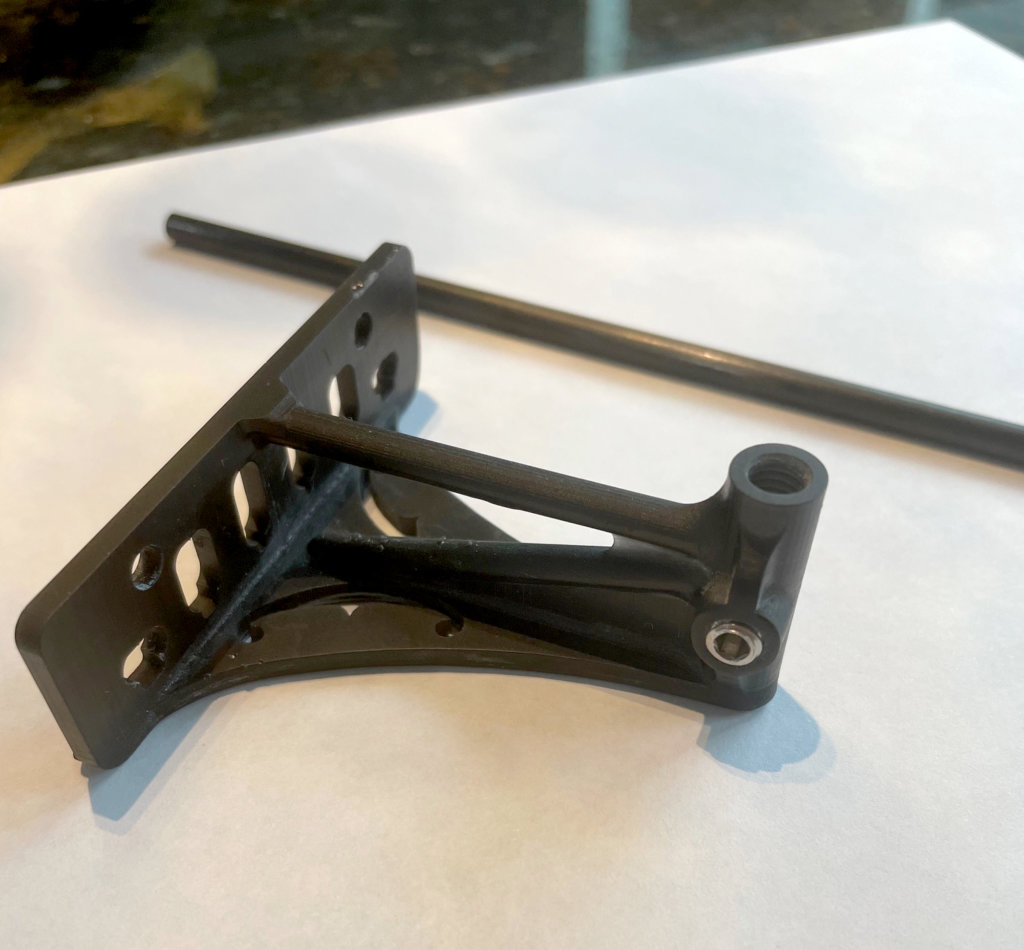
With the XiP desktop 3D printer, LST is able to print a batch of 60-70 pieces of The Droplet Sound System in about 30 minutes, and at a significant discount compared to their supplier. “Material cost per bolt with xCE on XiP is about 1/10th the cost of the finished bolts from our supplier in Taiwan, and that’s even with the high volume discount.” Vlad’s team has been able to significantly reduce overhead, while introducing an incredible amount of flexibility into their design / manufacturing cycle. Now an improved design can be developed, tested, and manufactured in just one month – a major improvement from the year timeline.
Bringing Products to Market with XiP
The success of The Droplet Sound System has led Vlad and team to identify new applications and products that could be both developed and manufactured using XiP. One of these products is their Bridge Doctor 2.0. Printed on XiP, Vlad says “it’s twice as light and twice as strong as the previous wooden version. We are able to print it using FDM since it is a larger piece, but XiP is about 10x faster and has superior part quality so we’ll probably be sticking with that.”
Desktop manufacturing with XiP has opened up new opportunities for Vlad and Liquid Sound Technologies. As a small business, it has provided them with flexibility to ramp production up and down and to quickly iterate to bring new products to market. “Next on the horizon is a piano system, and we’re also testing out some printed drum products.”